Müllanlieferung
Der Hausmüll, also der Restmüll aus den grauen Tonnen, wird in Müllsammelfahrzeugen angeliefert. Über eine Rampe erreichen die Müllfahrzeuge die Entladeplattform von einer der insgesamt 16 Abkippstellen. Sie befindet sich auf eine Höhe von 7 m über dem Bunkerboden. Das Rangieren und Abkippen passiert in einer geschlossenen Halle.
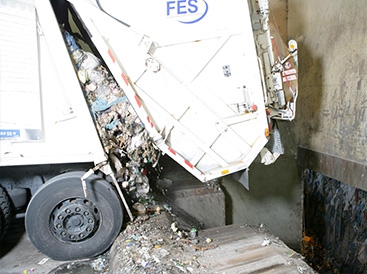